12 Ways to Maximize Warehouse Space Utilization
Warehouse space utilization is crucial to ensuring smooth operations and cost-effectiveness. Smart layout planning aligns reduces travel time, improves accessibility, and so increases total warehouse efficiency.
Efficient use of space not only enhances operational efficiency but also has a favorable impact on profitability. If you run out of inventory space in your distribution center for any reason, you have some good options for improving capacity without expanding. Let’s explore the 12 easy ways to maximize your warehouse space in this post.
Need help getting the most out of your warehouse space or developing your warehouse management system? Contact the experts at SPExpress for an efficient warehousing and order fulfillment solution. We will help you develop the best warehousing and handling alternatives for your business, optimize your order fulfillment process, and provide insights on how to improve your warehouse operations.
At SPExpress, we offer efficiency, scalability, and comprehensive warehousing solutions to businesses of any size, easing the burden on businesses. Contact us to find out more about how we can make warehouse management simple for your business today!
12 Ways to Maximize Warehouse Space Utilization
12 Ways to Maximize Warehouse Space Utilization
Assessing Warehouse Layout
A distribution center is technically out of space when it reaches 80 to 85 percent occupancy. Because that holds not only to warehouse storage, but also to receiving, shipping, and all other process areas.
Before making any improvements, evaluate your current warehouse layout to find out solution to maximize warehouse space is the first step. Identify areas of unused space or poor organization that may be impacting your warehouse’s capacity and utilization. Understand the current layout’s flow and use, including rack setup, slotting, picking, receiving, restocking, inventory management, packaging, and shipping. Include seasonal peak trends and a comprehensive volume analysis of inbound and outbound product movement. Once you’ve identified the main factors that impact warehouse space utilization and management, you’ll be able to better proceed and address any possible issues.
Organizing Inventory Efficiently
A well-organized inventory system makes things more accessible, minimizing time spent searching for them and optimizing the use of area to maximize warehouse space.
Implementing a just-in-time inventory system will enhance your inventory management by reducing excess inventory and freeing up valuable warehouse space. This approach guarantees that you only stock what you need, which reduces storage costs.
Keep in mind that inaccurate demand forecasting is the major cause of stockouts and overstocking, which can influence warehouse space utilization. By combining key information such as previous sales and demand trends, you can plan your inventory replenishment accordingly and guarantee that you are making the best use of available space to stock up on the goods you require.
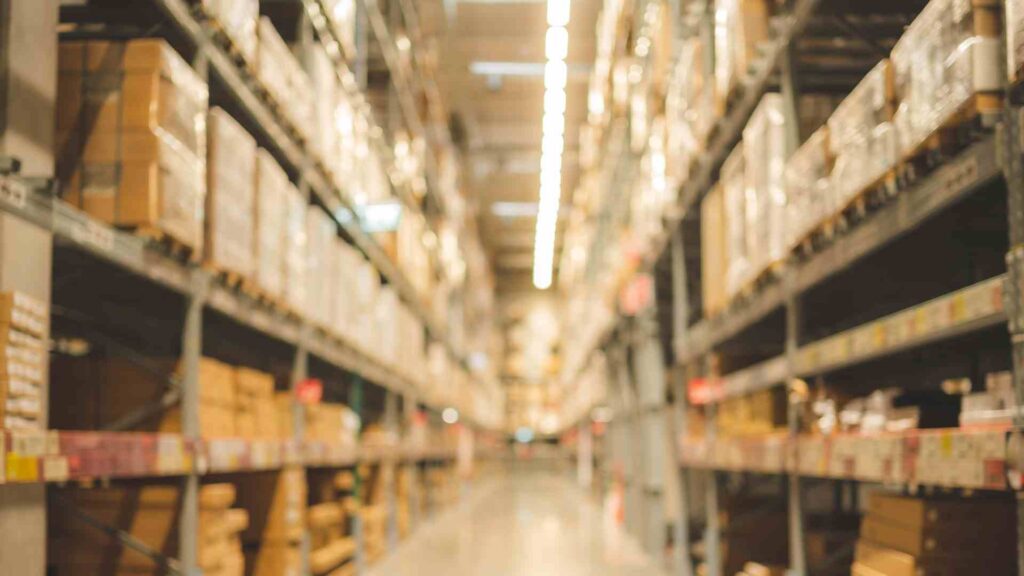
Utilizing Advanced Warehouse Management Systems (WMS)
Use cutting-edge WMS to streamline warehouse operations. Automation not only minimizes errors but also helps to maximize warehouse space based on product demand. An advanced warehouse management system allows you to manage your inventory more effectively, which improves the utilization of space.
Advanced WMS demand forecasting capabilities can help you better understand your inventory demands, allowing you to plan your replenishment orders more effectively and minimize overstocking. It enables real-time inventory tracking and inventory cycle counts, allowing you to maintain precise inventory levels and reduce the risk of stockouts.
Implementing Vertical Storage
Look up and make sure you’re making the most of the available vertical space. Vertical storage allows you to maximize the vertical space in your warehouse. Instead of reducing storage to floor space, shelves, and racks can be extended upwards to maximize the cubic feet available. Maximize warehouse space by investing in shelving and storage solutions that make use of your warehouse’s height. This minimizes unwanted sprawl and maximizes available cubic footage.
Expanding storage higher can significantly improve your warehouse’s overall storage capacity. This is especially useful for companies with a high amount of inventory because it allows them to store more products without increasing the warehouse’s physical space.
Optimizing Aisle Widths
Finding an optimal balance between aisle widths is important. Too small, it impedes mobility; too large, it wastes available space. For example, a wide aisle can be 10 to 12 feet long, but reducing it to five to eight feet can save 15 to 20 percent of the space.
Evaluate your traffic patterns and make necessary adjustments. Try to design the smallest width required to match the material handling equipment employed while maintaining operational efficiency.
Utilizing Racking Systems
Choosing the correct racking system is important for warehouse space utilization. A challenge in expanding racks in your distribution center is determining the optimum type of storage racks for the warehouse. Pallet racking, cantilever racking, and drive-in racking are examples of systems designed to meet specific storage requirements. Here are some of the most popular types of warehouse storage racks for maximizing warehouse space:
- Pallet Racks: Depending on your industry, your warehouse likely has already stocked with pallet racks. Using these basic racks in conjunction with a forklift and pallets is one of the greatest ways to maximize storage space if you have a wide variety of inventory types.
- Cantilever Racks: Cantilever racks are ideal for storing long-term inventory. These racks have projecting arms where inventory is put. When extending these racks, evaluate whether employees will require additional equipment to reach higher levels of goods.
- Drive-In Racking: Designed for high-density storage, these systems allow forklifts to drive directly into the storage lanes. Drive-in racking follows a Last-In, First-Out (LIFO) system.
- Carton Flow Racks: These racks are perfect for first-in, first-out (FIFO) inventory systems. Carton flow racks include slanted panels that push down older inventory, making it more accessible.
- Mezzanine Racking: Mezzanines are platforms that extend storage space to a second level above the warehouse floor. Mezzanines are another secret weapon for optimizing warehouse space.
Cross-Docking Strategies
If possible, try cross-docking major releases of back orders or single-line orders to reduce the volume of inventory that requires storage space. Cross-docking reduces storage time by directly transporting products from inbound to outbound segments, hence decreasing the requirement for massive storage spaces.
Cross-docking reduces the need to hold inventory by promptly loading received goods onto outbound vehicles for fulfillment. Adopting this method wherever possible will limit the amount of inventory that must be allocated to storage destinations. As a result, make the most of available space by holding inventory that needs to be held for longer.
Regular Space Audits
Perform regular audits to identify and resolve space wastage. This proactive approach ensures that your warehouse is always working at its maximum capacity. A regular audit of your warehouse and inventory is necessary for identifying issue areas, ensuring inventory accuracy, and developing an optimization strategy. During the audit, you may be able to find opportunities to reduce deadstock and slow-moving inventory, making a place for more profitable SKUs.
A full warehouse audit will allow you to analyze how your inventory is currently stored and whether there are any areas for improvement. For example, the audit process may discover damaged shelving systems that you cannot use for storing products. In this case, repairing or replacing those systems could greatly increase your space utilization.
Packaging Practices
Choose packaging materials that are most close to the size of the goods being transported. Avoid using excessively large boxes for smaller products because they waste storage space. If you need to store substantial supplies or packing materials, plan to keep track of the inventory to avoid overstocking.
Alternatively, talk to your corrugated provider to see if they can keep some inventory on-site for you and take deliveries every few days. Performing regular evaluations of packaging effectiveness will help you keep up to date with the changes in product size or packing materials could result in better space use.
Outsourcing Storage for Seasonal Goods
Consider outsourcing seasonal product storage to external facilities during peak seasons. This reduces overcrowding and keeps up smooth operations.
For example, many warehouses may bring in extra trailers and pay the demurrage penalty for temporary storage rather than expanding their facility during peak times. Storing merchandise in trailers is often a necessary solution for temporary warehouse storage. This is typical of seasonal products, particularly among merchants. If you store and transport large items, you might consider storing merchandise in trailers, outsourcing storage, or even using drop shipping to save in-house inventory and expenses.
Employee Training for Space Optimization
If you’re still using old training and protocols from years ago, you may run into difficulties with capacity in your warehouse. The chances are that your company has expanded over time, and your warehouse has either implemented new storage solutions or added new storage spaces to support this expansion.
Establish a responsible culture by educating your team on effective storage procedures. Well-trained employees recognize the value of space efficiency. Otherwise, your employees may lack the required knowledge to manage those alterations and improvements, limiting available space while also exposing warehouse security risks.
Continuous Improvement Strategies
There is no one ideal approach to solving warehouse capacity challenges at once. The solution is typically a combination of multiple factors. You might open up the area, and add equipment, and trailers to the yard. Execute regular space audits to determine how storage spaces are currently being used. Identify neglected areas, dead zones, or poor layouts.
The way to maximize warehouse space utilization is usually more than one answer. Encourage continuous enhancement to regularly examine and reassess your warehouse operations to remain flexible to industry developments. Set up continuous monitoring systems for storage conditions, picking rates, and overall warehouse performance. Analyze data regularly to find trends and areas for better improvement.
Implementing these strategies to maximize warehouse space will surely increase your warehouse space utilization, resulting in more efficiency and cost savings. A company can optimize space, increase productivity, and respond to changing needs by performing continuous improvements. Remember that the key is to continuously improve and innovate rather than simply implementing them once.
Need help getting the most out of your warehouse space or developing your warehouse management system? Contact the experts at SPExpress for an efficient warehousing and order fulfillment solution. We will help you develop the best warehousing and handling alternatives for your business, optimize your order fulfillment process, and provide insights on how to improve your warehouse operations.
At SPExpress, we offer efficiency, scalability, and comprehensive warehousing solutions to businesses of any size, easing the burden on businesses. Contact us to find out more about how we can make warehouse management simple for your business today!
Read more:
Shift From In-House To Outsourced Fulfillment – When it’s Better & How to Do it Right
How Third-party Logistics Services Can Ensure E-Commerce Growth?
The Top 6 Reasons For Outsourcing in Supply Chain Management For Your eCommerce Business
At SPExpress, we offer services from order fulfillment to supply chain management services that include freight forwarding, transportation, warehousing, picking and packing, inventory and supply chain management, and order fulfillment. We work closely with our customers to ensure their 3PL needs are being met properly. Since we understand how valuable working with a reputable 3PL provider can be, and how it can help our customers to focus on growing their businesses.